DFM & Mold Flow Analysis
- Selection Techniques for Plastic Mold Materials
- Basic Knowledge Of Injection Molding Process
- Differences Between Two Plate Molds, Three Plate Molds, And Hot Runner Molds
- Common Equipment For Plastic Injection Mold Tooling
- Standard Trial Process For Injection Molds
- Five Molding Processes For Injection Molding
YCH Mold adheres to a professional philosophy, helps customers optimize product structure, organizes core technical and R&D teams, conducts open communication and review with customers, maintains sufficient communication and exchange, solves customers’ product design problems, and provides new product manufacturing processes and multi- injection molding design concepts, striving to form the best mold design solution, making it easier for customers to occupy the market.
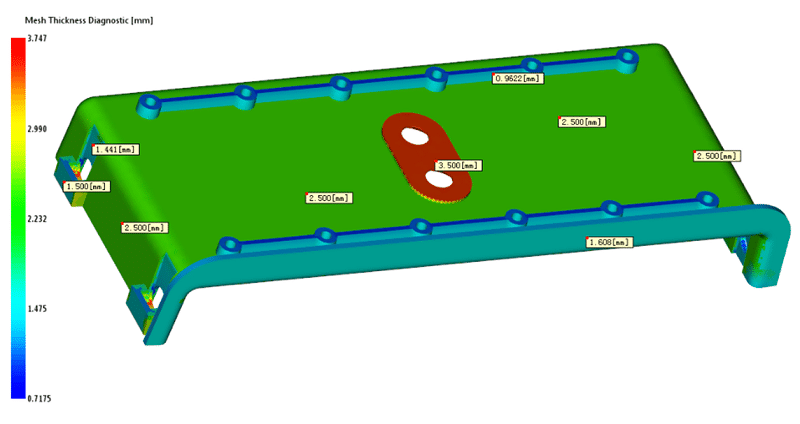
What is Mold Flow Analysis and its Benefits?
Mold Flow Analysis is an integral element of injection molding production. Engineers utilize special software to simulate and assess how plastic material flows inside of molds during manufacturing; by looking at factors like pressure, temperature, and cooling rates they can identify any potential issues before production commences.
One of the primary advantages of Mold Flow Analysis lies in its ability to anticipate and prevent manufacturing defects. By simulating various scenarios, designers can optimize mold designs to mitigate issues like air traps, warping or sink marks while increasing product quality while decreasing costly rework or scrap. This approach ensures both superior product quality and cost reductions associated with costly rework or scrap.
Mold Flow Analysis also can assist manufacturers by optimizing fill patterns and decreasing material waste – meaning faster production cycles and increased efficiency for manufacturing companies.
Mold Flow Analysis allows engineers to make more informed choices when it comes to material selection and gate placement, providing stronger parts with reduced imperfections. Through accurately forecasting how different substances flow through their mold cavity, engineers can make informed choices that lead to stronger parts with fewer imperfections.
Integrating Mold Flow Analysis into the design process results in more efficient production processes and higher-quality plastic components. By helping identify potential issues early, and saving both time and money later in production stages, Mold Flow Analysis is now considered an indispensable asset to successful injection molding operations.
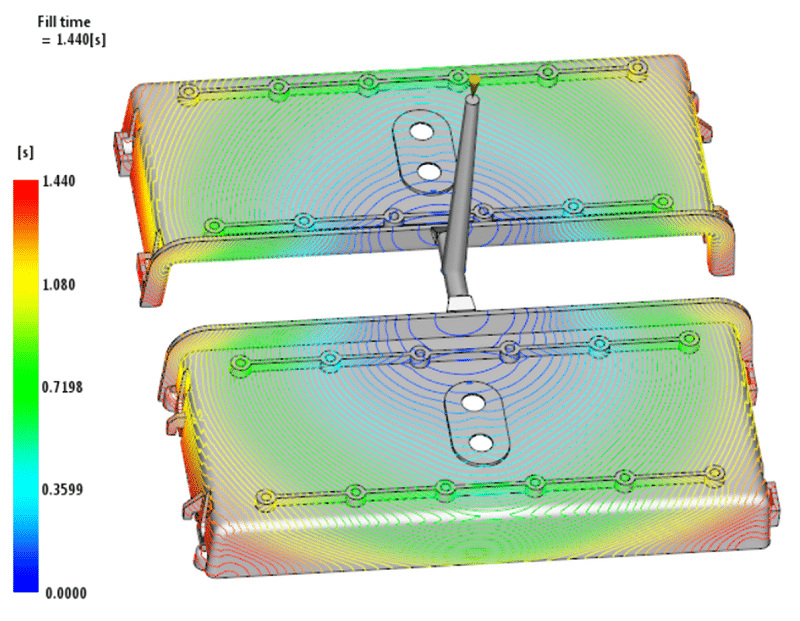
Importance of Mold Flow Analysis
Mold flow analysis plays an integral part of injection molding production, providing important insight and predictions into how plastic parts will behave during their creation process. By simulating how molten plastic flows within a mold, engineers can identify potential issues before they arise – thus saving both time and resources in production.
Mold flow analysis offers numerous advantages, one being its ability to detect potential defects like air traps, weld lines, or sink marks. Engineers can leverage factors like temperature distribution, pressure variation and material flow rate analysis in their designs in order to minimize these flaws and produce higher quality parts.
Mold flow analysis plays an integral part in cycle time optimization. By studying fill patterns and viscosity variations within a mold cavity, engineers can identify optimal gate locations and runner designs to achieve efficient filling, helping reduce cycle times while increasing overall productivity.
The Basics and Benefits of Design for Manufacturing
Design for Manufacturing (DFM) is an integral component of product development that ensures designs can be efficiently and cost-effectively manufactured. By considering manufacturability in early design stages, companies can avoid potential production issues while creating smooth production processes.
DFM (Design For Manufacturability) seeks to streamline manufacturing by eliminating unnecessarily complicated designs. This typically entails creating parts with easy assembly in mind, selecting materials readily available at cost-effective rates, and limiting component numbers accordingly.
Implementation of DFM principles has the ability to substantially lower production costs for companies. By designing products with easier manufacturing processes and streamlining assembly procedures, companies can save both time and money during production processes; additionally, this reduces assembly times which ultimately increases overall productivity.

DFM not only saves companies money but it can also lead to improved product quality by optimizing designs for manufacturability – which reduces errors or defects during production resulting in higher-quality goods that meet customers’ expectations.
DFM plays an instrumental role in shortening time-to-market for new products by taking into account manufacturing requirements early in their design phase, eliminating possible delays or redesigns later on, which allows companies to bring products faster to market than their competition.
Integrating Design For Manufacturing principles contributes significantly to sustainability by decreasing waste and improving resource utilisation during the production process. Designs featuring minimal material usage not only save costs but also lessen environmental impacts.
Adopting Design for Manufacturing can bring many advantages, including cost reduction, improved product quality, shorter time-to-market and increased productivity as well as enhanced sustainability practices. Adopting this methodology should be part of every company’s manufacturing operations strategy for efficient production that delivers top quality products efficiently.
Moldflow DFM for Producing High Quality Plastic Parts
Moldflow DFM (Design for Manufacturing) is an advanced software tool that plays an essential part in assuring high-quality plastic part production. Manufacturers using Moldflow DFM are able to simulate and analyze how molten plastic flows within mold cavities, helping identify any issues or optimizing designs before going into production.
Utilizing Moldflow DFM, engineers are able to accurately anticipate how injection molding materials will behave by evaluating fill time, cooling rate, warpage rate and sink marks — as well as other crucial parameters which impact part quality – that influence injection molding performance.
Moldflow DFM’s primary advantage lies in its ability to identify potential manufacturing issues early in the design stage, through simulating various scenarios and analyzing parameters, engineers can pinpoint areas for improvements that would enhance part performance while decreasing manufacturing issues.
Additionally, this software also enables designers to maximize gate locations and sizes within mold designs using simulation results from Moldflow DFM analysis. By strategically placing gates within their mold design using this methodology, manufacturers can improve flow characteristics while decreasing cosmetic defects like weld lines or air traps.
Moldflow DFM also provides invaluable insights into material selection by providing insight into how different polymers will perform during injection molding, helping users choose materials which suit specific applications while avoiding common risks associated with certain resins.
Moldflow DFM’s quality plastic part production services help streamline product development while cutting costs associated with rework or tool modifications later on. By anticipating potential manufacturing hurdles with simulation-driven optimization techniques provided by this powerful toolset – manufacturers are better able to produce higher quality products more quickly than ever.
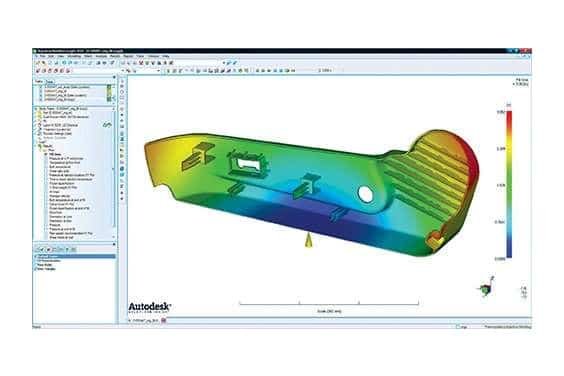
Conlusion:
Design for Manufacturing (DFM) and Mold Flow Analysis are critical practices in successful injection molding, helping identify any manufacturing challenges early in the design stage and leading to higher product quality and reduced rejection rates.
YCH Mold emphasizes the benefits of DFM to our clients with the knowledge that this powerful diagnostic tool will create a more efficient production cycle and ultimately increase profitability.
We are also able to address design issues at the earliest possible stage by using Moldflow® simulation software to identify critical information that helps avoid costly part redesigns, tooling changes or modifications, such as:
1.Fill patterns
2.Sink mark estimation
3.Warpage trends
4.Air trap estimation
5.Time & Pressures