Mold Manufacturing
- Selection Techniques for Plastic Mold Materials
- Basic Knowledge Of Injection Molding Process
- Differences Between Two Plate Molds, Three Plate Molds, And Hot Runner Molds
- Common Equipment For Plastic Injection Mold Tooling
- Standard Trial Process For Injection Molds
- Five Molding Processes For Injection Molding
Introduction:
YCH Mold builds a wide variety of Plastic Injection Molds, ranging in size from small M.U.D. inserts to molds of 15 tons; single cavity to multiple cavity; proto-type to high production class 101; standard runner/gates to hot manifolds with valve gates.
A. Overmold
The Overmold method is a plastic injection technique that seamlessly combines several materials into a single component. This technique gives the manufacturer more control over their product, and add a stylish finish as well.
B. Insert Mold
This form of molding is more varied, and involves the insertion of a metal part into a mold, before the actual instance of injection molding. Once the insertion is finished the mold is closed, and plastic is molded over the insert to transform it into a single component.
C. Plastic Injection Mold
Plastic injection molding is the process of directly injecting liquid plastic into the cavities of a specially made mold. This is a key service of Immould, and we provide various injection molding solutions to various industries.
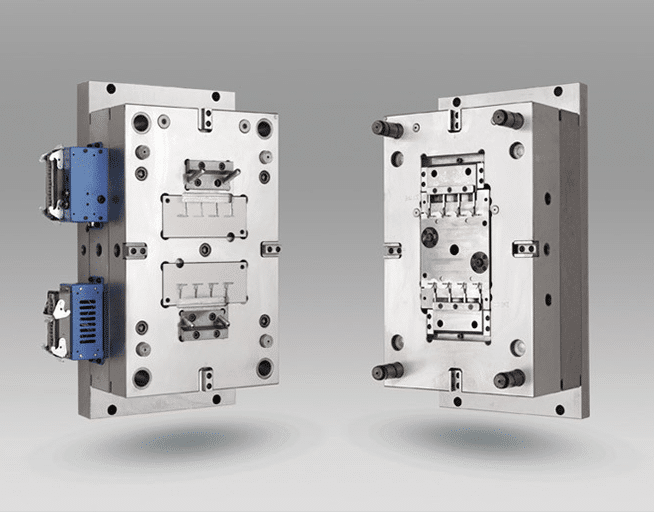
The Process of Plastic Injection Mold Manufacturing
The process of plastic injection mold manufacturing is a carefully orchestrated dance between precision and creativity. It begins with the design phase, where engineers meticulously craft the blueprint for the mold, taking into account factors such as material flow, cooling channels, and part ejection.
Once the design is finalized, it’s time to bring it to life. First, a block of steel or aluminum is selected as the base material for the mold. This block undergoes machining processes such as milling and drilling to shape it into the desired form. The next step involves creating cavities within the mold that will define the shape of each individual part.
To ensure smooth and accurate molding, these cavities are polished to a mirror-like finish using techniques like diamond polishing or EDM (Electrical Discharge Machining). This attention to detail ensures that every molded product will have consistent dimensions and surface quality.
With an immaculate mold in hand, it’s time for injection molding itself. The chosen thermoplastic resin is melted down and injected under high pressure into the cavity of the mold. Once cooled and solidified, it can be ejected from its respective cavity.
Throughout this entire process, quality control measures are implemented at every stage to ensure that each molded part meets strict specifications. From initial design verification through final inspection of finished products – no stone is left unturned when it comes to achieving excellence in plastic injection molding.
Innovation continues to drive advancements in this field – from computer-aided design software that streamlines prototyping procedures to automated robotic systems that enhance production efficiency. As technology evolves further, we can expect even greater precision in plastic injection mold manufacturing – pushing boundaries beyond what was once thought possible.
Plastic injection molding has become an essential manufacturing technique across various industries due to its versatility and cost-effectiveness. Whether producing intricate medical devices or everyday consumer goods – there’s no doubt about its impact on our daily lives.
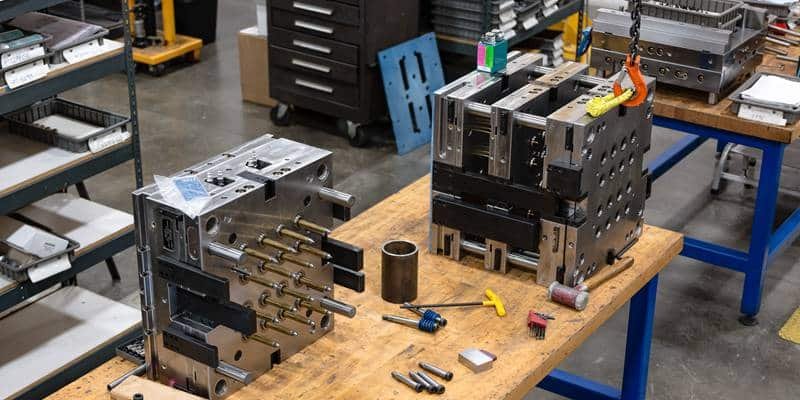
Plastic Injection Mould Manufacturing
Start from request analysis or product design analysis.
Mold design drawing and DFM report available.
Mold flow report will be sent.
Ensure your mold quality in high quality, less mold repair.
Fast delivery, it takes 15-25 working days to make mould, precise time depends on part design.
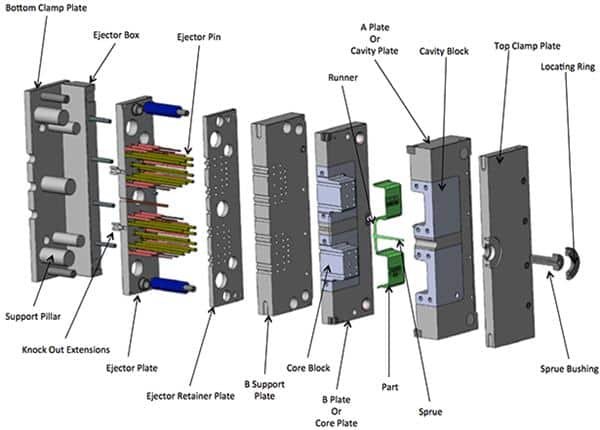
Mold inspection and trial
- Inspection of molds
The process of fit molding and assembly can actually be considered as an inspection process for the mold. During fit molding assembly, it is possible to check whether the red lead is in place, whether the ejector pin and cylinder are smooth, and whether there are any errors in the mold that interfere with the assembly process. - Trial mold
After the mold manufacturing is completed, in order to detect the condition of the mold and whether the structure of the rubber parts is ready, it is necessary to test the mold on the injection machine. Through the test, it is possible to understand the conditions of the mold during the molding process and whether the structure of the rubber parts is ready.
For the requirements of mold testing and the improvement of rubber defects, please refer to other documents.
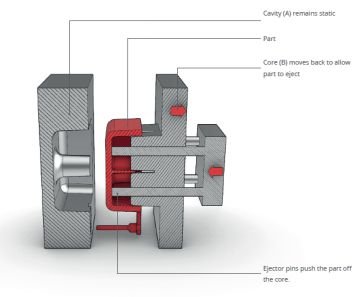
Mold Tooling Equipment:
The production of precise and high-quality metal molds cannot be separated from high-end manufacturing equipment and a production environment with constant temperature and humidity. To meet these conditions, YCH Mold has specially constructed a 10,500 square meter bright air-conditioned mold production workshop.
Our workshop has various processing and manufacturing equipment for molds, including precision machining processes such as slow-moving wire cutting, surface grinding, molding grinding, and high-precision component micro-drilling.
YCH Mold has CNC machining centers from world-renowned brands such as OKUMA, MAKINO, ROKUROKU, YASDA, and FANUC, as well as EDM machines from world-renowned brands such as AGIE and MAKINO, to meet customers’ high-precision and high-quality processing needs for precision plastic product molds.


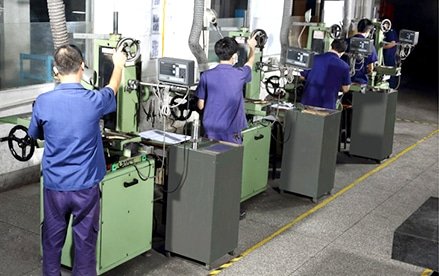
serial number | Device name | brand | Processing stroke | Accuracy | quantity | Notes |
1 | CNC machining center | OKUMA | 1050*560*450mm | ±0.0080mm | 5 | 14 units in total |
MAKINO | 650*400*400mm | ±0.0080mm | 2 | |||
ROKUROKU | 600*500*400mm | ±0.0080mm | 2 | |||
YASDA | 600*400*350mm | ±0.0025mm | 1 | |||
FANUC | 500*400*330mm | ±0.0025mm | 2 | |||
CTM | 1000*700*600mm | ±0.0050mm | 2 | |||
2 | Sparks | AGIE | 350*300*400mm | ±0.0050mm | 6 | 11 units in total |
MAKINO | 500*400*400mm | ±0.0050mm | 5 | |||
3 | wire cutting | AGIE | 350*250*250mm | +0.0030mm | 4 | 4 units in total |
4 | Precision form grinding machine | OKAMOTO | / | / | 6 | 6 units in total |
5 | grinder | BATAR | / | / | 6 | 6 units in total |
6 | milling machine | BATAR | / | / | 6 | 7 units in total |
LAGUN | / | / | 1 | |||
7 | hole puncher | Numerikon | / | / | 2 | Total 2 units |