Injection Molding
- Selection Techniques for Plastic Mold Materials
- Basic Knowledge Of Injection Molding Process
- Differences Between Two Plate Molds, Three Plate Molds, And Hot Runner Molds
- Common Equipment For Plastic Injection Mold Tooling
- Standard Trial Process For Injection Molds
- Five Molding Processes For Injection Molding
We have the world’s leading 3D printing, numerical control processing, vacuum composite molding, low-pressure infusion, injection molding and other equipment. Our rich production experience can provide you with services from product design to prototype verification, rapid mold manufacturing to small batch trial production and mass production.
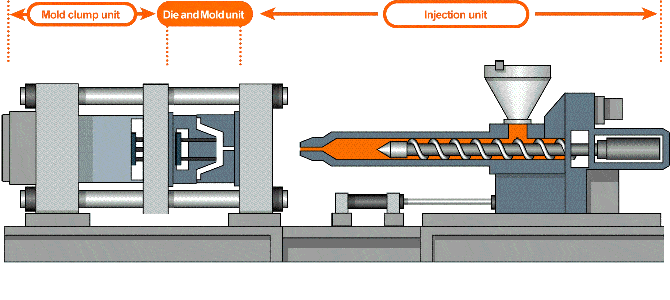
Benefits and features of our plastic injection molding services:
Advanced Mold Design and Engineering: our design professionals create intricate molds of specific products.
Materials Selection Skills: Knowledge and expertise in selecting suitable thermoplastic or thermosetting polymers.
Quality Control: YCH Mold Employs strict quality checks throughout production process.
Technical Support: YCH Mold Provides engineering expertise and design assistance to optimize manufacturability and cost-efficiency.
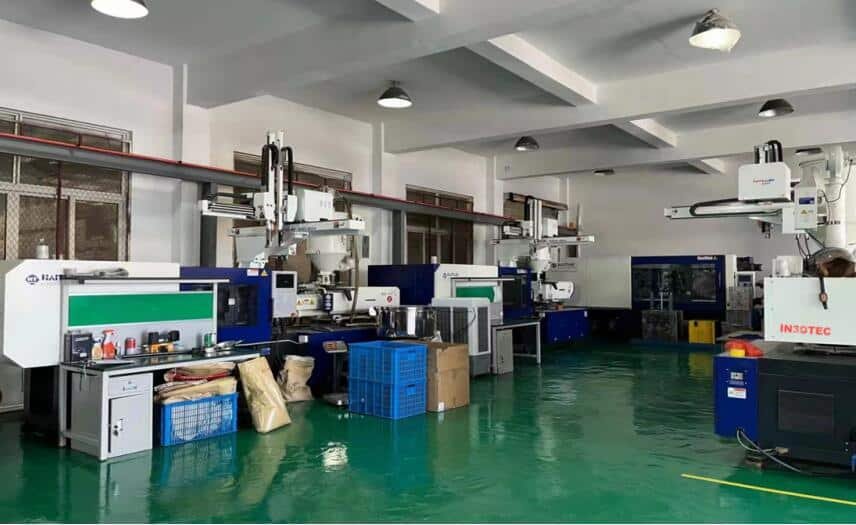
Common Applications of Injection Molding
Injection molding is an innovative manufacturing technique used in multiple industries and applications ranging from consumer goods production to automobile components manufacturing. As an economically and time-effective method of producing quality plastic components at reduced costs, injection molding offers numerous advantages when used within these contexts.
Consumer goods industries utilize injection molding technology extensively when producing items like food containers, packaging materials and toys. With its ability to reproduce intricate details while shaping complex shapes, injection molding makes an excellent solution.
Automotive industries rely heavily on injection molding technology for producing components like interior trim, dashboard panels and engine parts that offer durability and precision – essential assets in this competitive sector. Molded parts offer lasting precision.
Medical devices likewise take advantage of injection molding technology due to its capacity of producing sterile, accurate parts like syringes, IV connectors, and surgical instruments that can be manufactured consistently through this process.
Electronics manufacturers utilizing injection molding technology employ housings for smartphones or laptops which offer protection from external factors while remaining aesthetic – this ensures robust devices while keeping aesthetic value.
Aerospace, construction and sports equipment industries all utilize injection molded parts due to their superior strength-to-weight ratio properties.
Injection molding’s application spans across numerous industries and applications. Due to its flexibility, injection molding effectively meets diverse customer demands with tailored solutions designed specifically to their requirements.

The Process Of Plastic Injection Molding: Step by Step
Plastic injection molding can be a complex process with many steps involved to meet the specifications you set forth for a product that fulfills all the specifications you set. Here is an outline of each stage:
Step 1: Design and Prototype
Before production can commence, manufacturers use computer aided design (CAD) software to draft up an elaborate plan which they use as the blueprint to develop prototypes that they test before moving ahead with mass production.
Step 2: Mold Tooling
Once a design has been finalized, a mold must be created using its template as the starting point. Molds often consist of either steel or aluminum materials and consist of two halves: injection side (i) and ejector side (ii).
Step 3: Material Prepation
Once the mold has been prepared, it’s time to prep its contents. Plastic pellets are fed through a hopper into a heated barrel where heat melts them to their liquid state, until ready for injection into the mold.
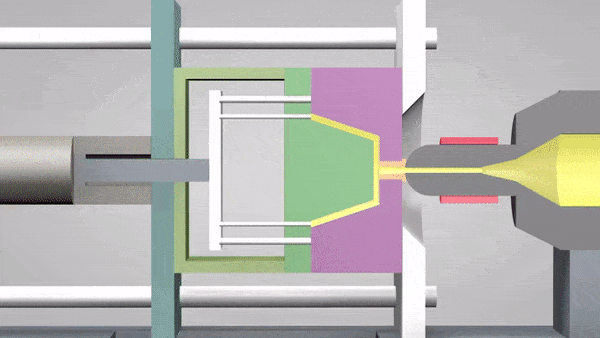
Step 4: Injection
Once your plastic has set up, its time for injection. Melted plastic will be forced through an injector into a mold cavity under high pressure through an attached nozzle connected to an injection unit and into its cavity.
Step 5: Cooling and Solidification
Once plastic material has been injected into a mold, cooling channels within help quickly cool it down and solidify quickly so as to achieve precise dimension accuracy for its finished product. This step ensures maximum productivity from production.
Step 6: Ejection
Once adequate cooling time has lapsed, hydraulic cylinders apply force on either side of the mold in order to release its contents by way of pins or plates pushing against one side while pins/plates apply pressure against another side to release its part from it and push against one of them as an ejecting pin/plate is pushed against. This releases it from its confines of being trapped inside.
Step 7: Finishing Touches
Post-production can include trimming excess flash or adding any necessary finishing touches after ejection if required.
Plastic injection molding involves several basic steps; every project may have additional considerations depending on complexity or customization needs. Understanding this process is vitally important to both manufacturers and customers in ensuring its successful execution, leading to optimal outcomes and mutual success.
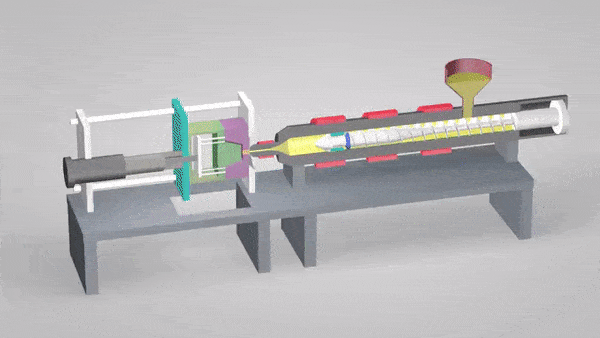
Plastic Materials Used in Injection Molding (IM)
Plastic injection molding is an exciting manufacturing process capable of creating diverse products. A key factor to ensure successful injection molding is choosing an ideal plastic material type to match with each application, each having different properties and traits that determine its success in injection molding. There are various plastics commonly utilized by injection molders – each having distinct advantages in terms of production efficiency.
Polypropylene (PP), one of the more frequently-used plastics used for injection molding applications, stands out for its excellent chemical resistance and impact strength – ideal qualities that make it suitable for automotive parts, packaging containers and household appliances.
ABS plastic offers both mechanical strength and dimensional stability, making it a go-to material in industries like automotive, electronics and consumer goods production due to its ability to withstand high temperatures while protecting from impact damage.
Polycarbonate (PC) plastic material is widely known for its transparency and exceptional toughness, making it suitable for various uses like eyewear lenses, medical devices, electrical components, and automotive parts.
Polyethylene (PE) comes in various forms such as low-density polyethylene (LDPE) and high-density polyethylene (HDPE), each offering different qualities: flexibility vs rigidity. PE materials are widely utilized for packaging films, bottles, pipes toys and artificial joints in medical devices.
Polyvinyl chloride (PVC) is known for its incredible longevity when exposed to weather elements like sunlight or moisture absorption, such as being UV exposed or having its moisture absorbers filled up by absorption from rainwater sources. PVC finds use primarily as construction material such as pipes or profiles as well as electrical cable insulation thanks to its flame retardant qualities.
Here are just a few types of plastic that can be utilized successfully during injection molding processes, depending on factors like desired product characteristics – like strength or flexibility – environmental conditions it will be exposed to (such as temperature fluctuations), cost considerations and regulatory requirements specific to certain industries.
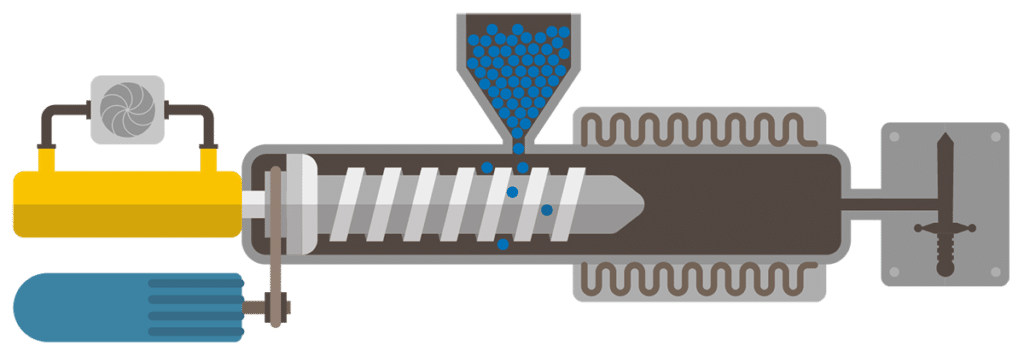
Factors to Consider Before Choosing a Plastic Injection Molding Company
Experience
When selecting a partner for your plastic injection molding project, experience should always be a factor.
Production Capacity
Before making your selection, be sure to evaluate each company’s production capacity carefully in order to assess whether they meet your project requirements.
Quality Control
Plastic injection molding companies that adhere to industry standards in their production must possess stringent quality controls measures throughout their production processes – this should include inspections and tests as part of quality checks for production.
Material Selection
To meet the specific demands of your project, ensure the injection molding company offers a range of materials that suit its design capabilities as well as meeting functional goals.
Customer Support
Technical support in case of unexpected circumstances or changes is an integral component of working with an injection molding partner, so they should provide it when required.
Location and Logistics
When selecting an injection molding company, take into account their location and logistics capabilities. Are you working under tight deadlines? Consider choosing one near by to reduce shipping time and costs.
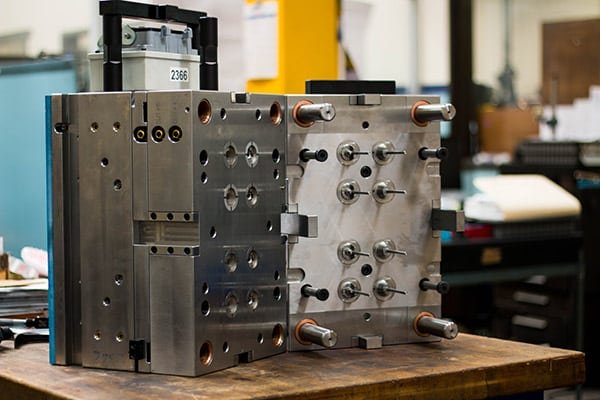
Price
Finding an economical solution to your plastic injection molding needs is of course important; however, be wary of companies offering lower prices at the expense of quality. Look for providers offering competitive pricing without compromising product integrity.
Communication and Collaboration
Look for a company that values open lines of communication with its customers so your project runs more efficiently from inception to completion. This will help ensure a more rewarding journey from its inception.
Referencing and Reviews
Do not be afraid to request references and read reviews written by past clients in order to gain further insight into a company’s reputation, customer satisfaction levels, and overall performance. Doing this may provide valuable data about its methods of management, levels of customer service it offers its customer base, as well as any overall performance indicators.
Because of our prompt,organized and specialized team, YCH Mold can offer the low cost quotation for your project , and make it within a short period; the price depends on the size,quantity,structure and materials ,we can offer good prices with quality products.We can make the first small batch products in 15 days after we got the PO; and we should submit to you the quotation in 3 days when we get your RFQ.