Mold Parts Processing
- Selection Techniques for Plastic Mold Materials
- Basic Knowledge Of Injection Molding Process
- Differences Between Two Plate Molds, Three Plate Molds, And Hot Runner Molds
- Common Equipment For Plastic Injection Mold Tooling
- Standard Trial Process For Injection Molds
- Five Molding Processes For Injection Molding
Each mold factory typically develops process standards tailored specifically for them in order to ensure the rationality and consistency of their mold production processes, optimize processing technology and increase manufacturing progress.
Mold Parts Processing Services from NTS include the creation of various mold components – cores, cavities, inserts and slides that form part of an assembly to form mold assemblies.
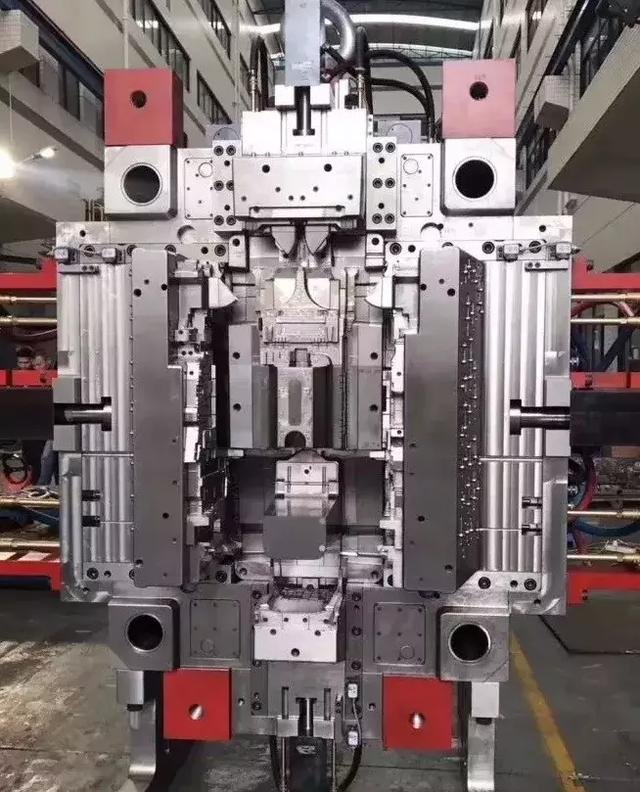
The key aspects of our mold parts processing services:
1.Precision Machining: Employing high precision techniques such as CNC machining, EDM (Electrical Discharge Machining), and other high-precision approaches such as Rapid Prototyping to produce accurate mold components within tight tolerances.
2.Material Selection: Our experts possess considerable expertise in selecting appropriate materials such as tool steel, aluminum or other alloys based on factors like durability, heat resistance and surface finish requirements.
3.Customization: Offering tailored solutions that fit specific design specifications, whether that means developing intricate features or unique geometries in mold parts.
4.Quality Control: Our quality checks and inspections during manufacturing ensure compliance with specifications and standards, thus guaranteeing reliable mold parts that perform to expectations.
5.Collaborative Design Support: Provide engineering expertise to optimize design for manufacturability, including using value engineering strategies that enhance cost-effectiveness and functionality.
6.Efficiency and Lead Times: With efficient production scheduling and execution to reduce lead times for delivery of mold parts on schedule for customer production timelines.
7.Post-Processing Services: Offering additional services like surface finishing, heat treatment, and coating application in order to increase durability and performance for mold parts.
8.Documentation and Tracing: For maximum transparency and future maintenance or reordering ease, providing comprehensive documentation and traceability is of utmost importance for each manufactured mold part.
As part of their comprehensive Mold Parts Processing service, plastic injection mold manufacturers can assist their clients in producing consistent and high-quality production results, leading to successful plastic injection molding operations.
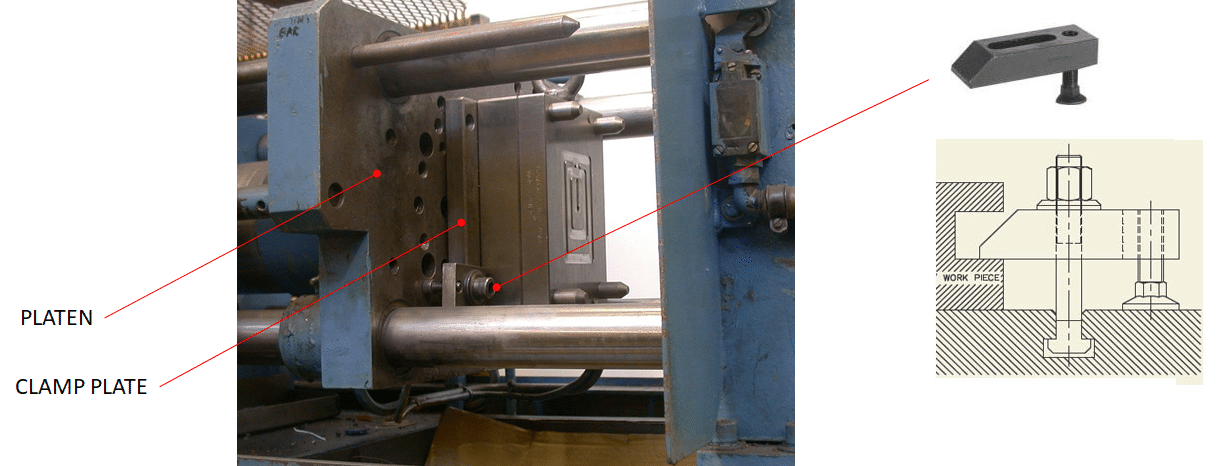
What Is Mold Parts Processing?
Mold parts processing is a specialized manufacturing technique for creating high-quality components using molds made of metal like steel or aluminum, providing hollow cavities into which materials such as plastic or metal may be injected or poured to take shape and take shape.
Starting the process involves designing and fabricating of the mold itself. Experienced engineers carefully craft this tool so it fits with all desired specifications of the final part to produce many identical copies efficiently and precisely. When completed, this faithful replication tool becomes capable of producing multiple identical copies quickly.
One popular method used in mold parts processing is injection molding. This technique involves injecting hot molten material under high pressure into a mold and watching as it cools and solidifies into its exact form dictated by its surroundings within.
Blowing molding is one of the primary techniques used for producing hollow objects such as bottles or containers, such as air blowing into a thermoplastic tube within a mold until its airflow expands it until filling all contours before being hardened and cooled off.
Mold parts processing offers many advantages over other manufacturing techniques, from mass production with exceptional precision and repeatability, all the way down to replicating complex shapes accurately for industries requiring intricate components.
Mold parts processing offers efficient production while simultaneously being cost-efficient by minimizing waste materials through meticulous material usage control during each cycle.
As technology rapidly develops, mold parts processing will continue to experience revolutionary innovations. From 3D printing techniques tailored specifically for molds to artificial intelligence algorithms that enhance quality control measures – emerging technologies promise to revolutionise this illustrious field of manufacturing.
Now you understand what constitutes mold parts processing, we will delve deeper into its fundamental principles as part of a successful implementation in our next blog section!
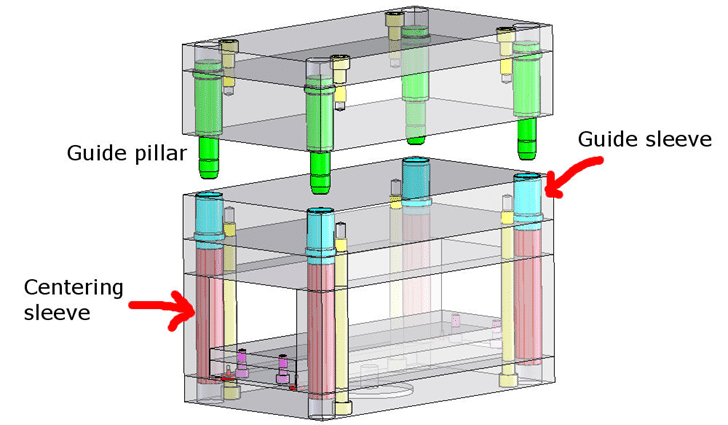
Techniques We Used in Mold Parts Production:
Mold parts processing involves employing various techniques in order to facilitate efficient and precise production, depending on the complexity and materials being used to make parts. These may vary according to part complexity or materials utilized.
One popular technique of injection molding entails injecting liquid material directly into a mold cavity for high production volumes and precise control over part dimensions. Another approach, known as blow molding, can create hollow products like bottles or containers more cost effectively than injection molding does.
CNC machining is often utilized when producing more intricate mold parts, providing precise cuts and shapes in metal or plastic materials like metal. 3D printing also has become an innovative approach in mold parts processing as it offers fast prototyping while simultaneously decreasing waste production.
Electroforming can be used for producing complex shapes with great accuracy. This process entails depositing metal onto an object using electrochemical deposition.
Each technique offers distinct benefits when processing mold parts. Understanding your project requirements allows you to select the technique with maximum potential to deliver successful results.
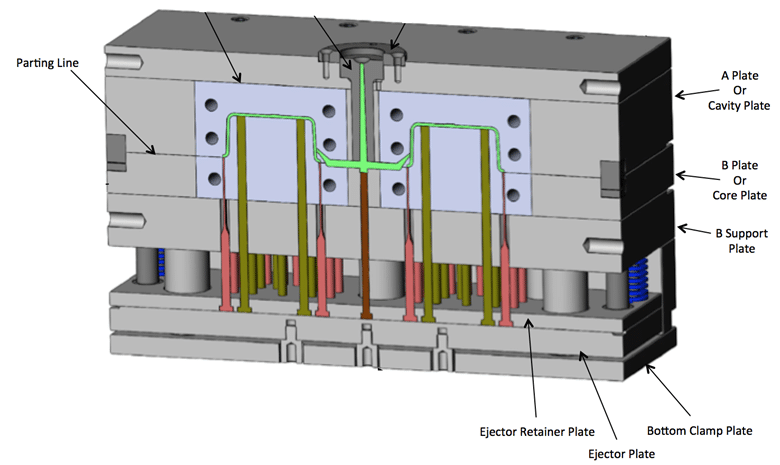
Key Considerations for Effective Mold Parts Processing
Mold parts processing requires careful consideration for optimal success, with materials selection playing an essential part. Selecting appropriate materials impacts not only quality but also durability and longevity of finished products.
Design optimization should also be prioritized when developing mold parts. Optimizing their designs to increase efficiency while decreasing defects or waste is of utmost importance; this includes features like cooling channels, ventilation ducts and optimal gate locations for example.
Maintaining effective process control throughout all stages of mold part manufacturing is equally essential to producing consistent results. Temperature, injection pressure and cycle time must all be closely observed so as to achieve uniform outcomes.
Communication among all participants involved – designers to manufacturers – cannot be underestimated. Effective dialogue prevents misinterpretations of data that could result in delays or additional work being necessary, leading to errors that require costly delays and reworks.
Regular inspection and maintenance of molds is key for their successful processing, helping prevent contamination or wear-and-tear that might affect product quality. Cleanliness also plays an important role.
By taking into account these key considerations when processing mold parts, your chances of producing high-quality molds and finished products without sacrificing efficiency or cost-efficiency can increase significantly.
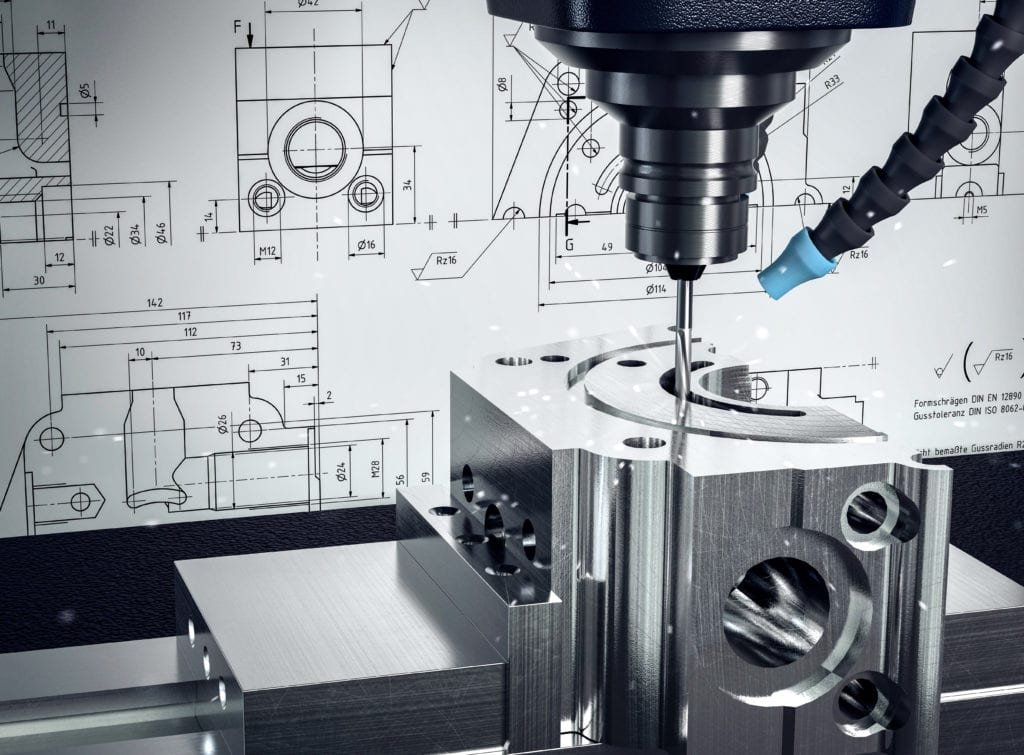
Our Mold Parts Processing services’ features:
- Precision Machining: Utilizing advanced CNC milling, turning and grinding techniques, precision machining produces mold parts with tight tolerances and precise dimensions.
- CAD/CAM Capabilities: Our staff employs computer-aided design (CAD) and manufacturing (CAM) software to ensure accurate production of mold components according to digital models and specifications.
- Material Knowledge: Proven expertise working with various materials ranging from tool steel, aluminum and specialty alloys in order to meet specific performance and durability criteria of mold parts.
- Customization Options: Offering tailored solutions that accommodate unique design features or special requirements of mold parts for customer flexibility in meeting various customer demands.
- Quality Assurance: Implementing stringent quality control measures throughout the production process, such as inspection protocols and tests to uphold high standards of precision and performance.
- Quick Turnaround Times: Our commitment to efficient production scheduling and lead times ensures timely delivery of mold parts, supporting project timelines and production schedules of customers.
- Collaborative Design Support: Offering engineering expertise to improve mold part designs for manufacturability and identify potential opportunities for cost savings or performance enhancements.
- Surface Finishing Services: Provider of optional surface treatments, polishing and coating services designed to increase mold part durability, wear resistance and functionality.
- Documentation and Tracing: Our goal is to maintain comprehensive documentation and traceability on each manufactured mold part manufactured, guaranteeing transparency while simplifying maintenance and reordering processes.