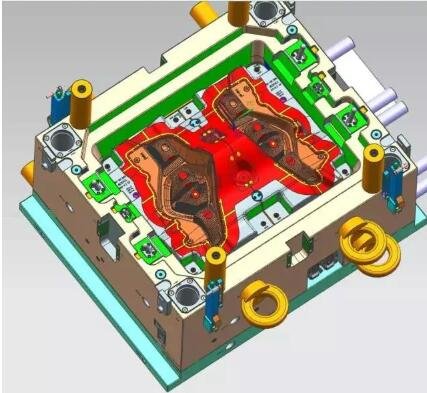
Analyze the structure and technical requirements of plastic parts. Pay attention to the dimensional accuracy, surface roughness requirements, and structural form of plastic parts. Suggest improvements to the plastic design for unreasonable structures.
2) Understand the technical specifications of the injection molding machine. This includes clamping force, maximum mold capacity, mold opening distance, size and position of ejection holes, mold placement method, flange dimensions, and other machine parameters.
3) Understand the processing and process performance of plastic materials, including the maximum flow distance ratio that can be achieved by plastic parts; possible crystallization, orientation, and internal stress caused by plastic in the mold; cooling shrinkage and shrinkage compensation of plastic; and the requirements of plastic for mold temperature.
4) Understand the customer’s specific technical requirements, and if they differ from the company’s standards, negotiate with the customer to resolve them.
5) Consider the structure and manufacturing of the mold, including the selection of parting surfaces and cavity layouts, as well as feed points; the strength, rigidity, and dimensional accuracy of the mold cavity; the positioning mechanism and ejection system; the manufacturing methods and scientific feasibility and economics of mold parts; the processability of assembly and disassembly; and the design of necessary auxiliary tools.
6) Consider the selection of mold materials, including the mechanical and process properties of the materials, heat treatment requirements, and the size of the material blank.
7) Consider the molding efficiency of the mold and set up water transport reasonably.