How can we encourage other industries to adopt metal additive manufacturing (AM) more and successfully push this technology into mass production? These are key goals for driving continued investment in additive manufacturing technology. We have our own views on the future progress of additive manufacturing applications from the perspectives of cost, quality, and ease of development.
Although there are many examples of small and medium-sized production of non-critical components, are we ready to meet the specialized and urgent needs of the maintenance, repair, and operation (MRO) market? In addition, can we meet the urgent needs for innovation and high-performance design in the aerospace and energy fields? Can we expand production scale as needed?
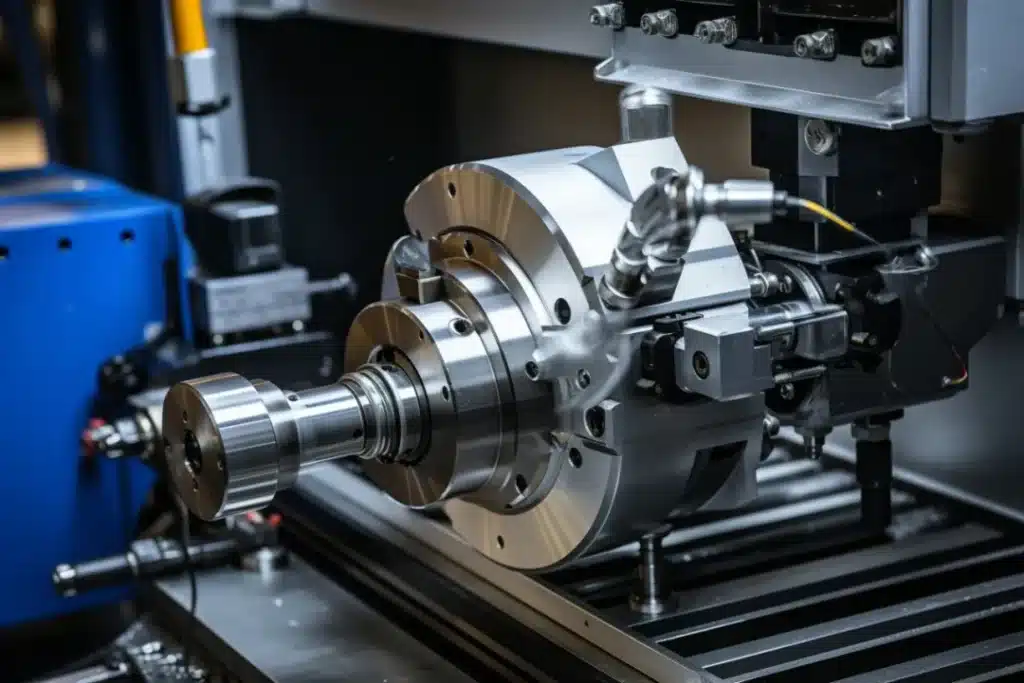
My answer: we still have much work ahead.
From laser powder bed fusion (LPBF), directed energy deposition (DED), and metal binder jetting (MBJ), automated metal forming technology continues to advance rapidly; yet several fundamental issues still persist, particularly cost, repeatability, and development issues.
1.Cost and its value curve
Not every component in a final product provides equal performance value; some features (shells and casings), while components like impellers or jet engine turbine blades require costly materials, making their production more challenging, as well as significant engineering resources to manufacture them. But complex parts can set apart your product from rivals by differentiating its overall worth from competing alternatives.
Additive manufacturing technology can also be used to produce parts which cannot be made with casting, machining, or traditional methods such as injection molding – adding significant value.
Therefore, the improvement of the functionality of additive manufacturing parts can often justify higher direct costs. However, what will the future of additive manufacturing costs look like, and how should we consider the cost of finished parts?
Using LPBF as an additive manufacturing cost and value model, we can currently say that materials (here referring to powdered metals) account for approximately 20-50% of the cost of finished parts, depending on the alloy used. Powdered aluminum alloys cost less than $50 per kilogram; GRCop-42 may cost more than $300 per kilogram, and refractory materials may cost thousands of dollars per kilogram.
Given the wide range of possible engineering decisions, the relationship between materials and costs results in production costs for metal additive manufacturing components ranging from $150 to $1,000 per kilogram.
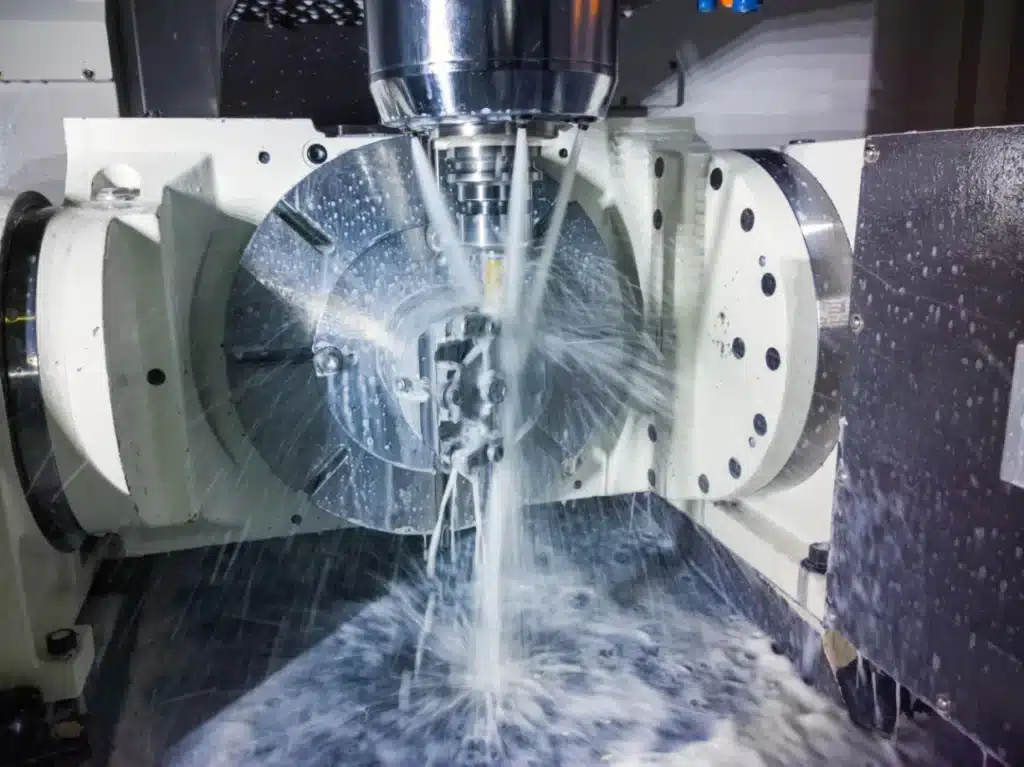
Answering this question properly involves considering value density (relative to weight and density). For instance, an ultra high-end car with a retail price of approximately $50,000 and weight of 2,000 kilograms has an approximate value density of $25 per kilogram.
A Boeing 737 MAX airliner weighing 40,000 kilograms possesses an approximate value density of $2,500 per kilogram – 100 times greater than what would be charged per kilo for cars.
Although the value of weight reduction in cars may change with new environmental regulations, weight reduction in aircraft is still more important. During the service life of an aircraft, using lightweight and lightweight materials such as composite materials is sufficient to offset material and manufacturing costs, just from the perspective of fuel savings.
The value density formula for stationary natural gas power plants cannot be compared to cars or aircraft, but improving the efficiency of energy turbines, as additive manufacturing has done on aircraft engines, will greatly increase the cost performance ratio of turbine components. Breakthroughs in thrust and efficiency of advanced rocket engines (achieved through additive manufacturing) have significant economic benefits in fuel savings, capability enhancement, and increased payload.
In these cases, innovation directly translates into higher unit cost value. So, given these values, why hasn’t additive manufacturing been more widely applied?
2.Cost, value, repeatability and industry-adopted qualification factors
We know that reducing the cost of additive manufacturing will continue to improve the value proposition of this technology, but what else can be done to promote the value equation and further promote its application? Improve qualification.

Qualification challenges involve the ability to produce parts with repeatable material properties and repeatable dimensional and geometric accuracy. When we say repeatability, we refer to repeatability between machines, year after year, and between suppliers.
Computer Numerical Control (CNC) machining has solved this problem. Similar solutions are just what additive manufacturing needs to gain recognition.
The industry expects similar and repeatable results from additive manufacturing. This proven standard is also the foundation for implementing continuous improvement and is the key to exploring deep innovation in additive manufacturing systems.
For example, hundreds of service providers develop inherent manufacturing processes that are difficult to achieve repeatable specifications. The problem stems from the machines of equipment manufacturers, where there are variations in the core processes and controls. Over time, machines can drift from their calibrated specifications, which means that the printing parameters of different machines can vary. After successfully printing on machine A, producing parts on machine B means that the certification process has to start from scratch.
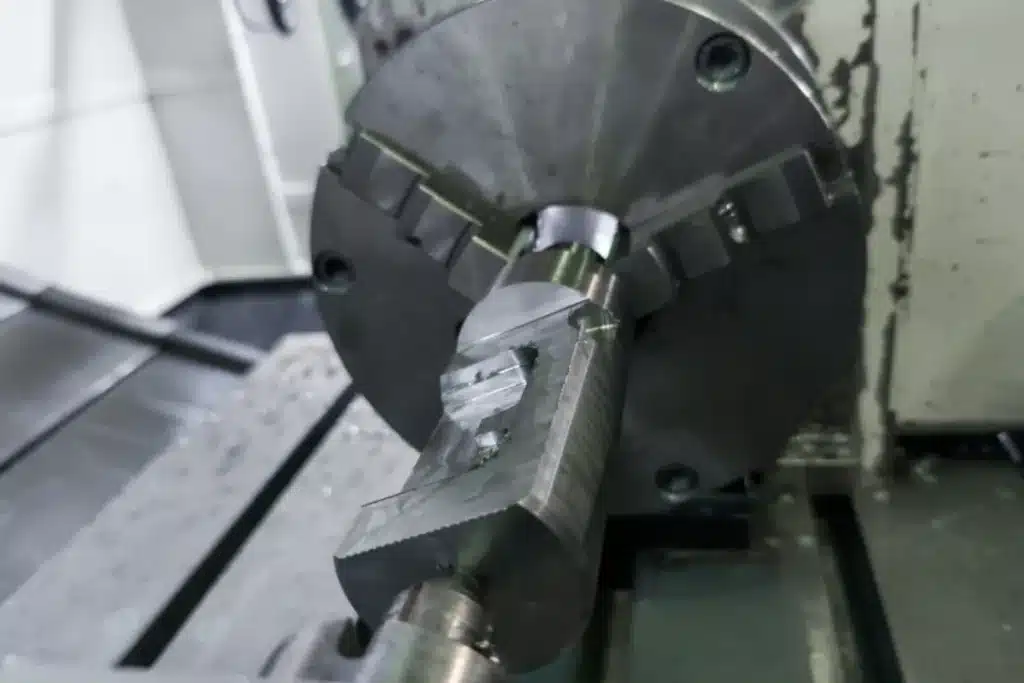
In 2024, in a distributed production project, the same valve was printed at six different locations – demonstrating the potential of using common print files to achieve target quality and scale production
Every new part requires process innovation, adjustment, and adaptation for each machine used to manufacture it. In other words, it is a constant reinvention of the wheel.
How can it be cost-effective? How can it achieve scalability? And ultimately, how can it realize mass production and broader industry applications organically?
3.Complexity of development affects training and education
The challenges faced by additive manufacturing development are closely related to qualification issues.
Developing alternative methods is required for manufacturing parts, so design for additive manufacturing (DFAM) is needed to produce the required parts.
Today, the structural limitations of additive manufacturing force engineers to apply DFAM rules to most designs to compensate for the lack of system printing capabilities.
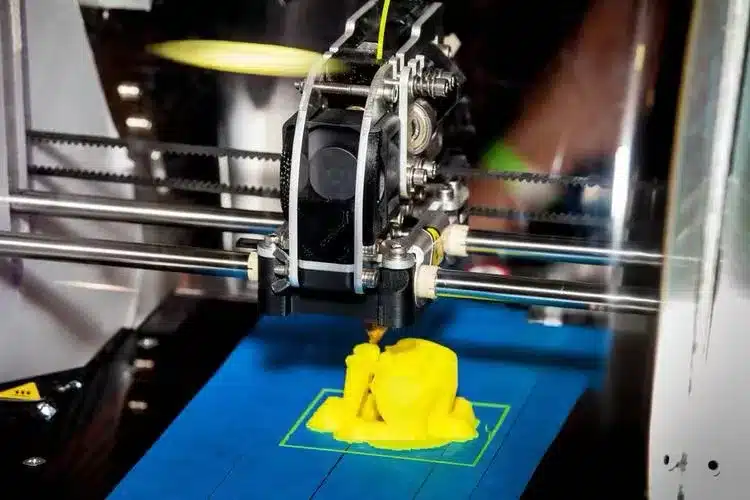
Similar to the challenge of identifying adjustments that must be made to files based on the printer in traditional additive manufacturing, development issues mean that in addition to adjusting the design, new technologies must be applied to make parts printable.
This method should be simplified using the general manufacturing and general calibration settings specified by the software, rather than circumventing machine limitations through ad hoc experimental adjustments.
This will directly benefit engineers who intend to adopt additive manufacturing. The inherent, built-in quality and inherent process fidelity can meet and verify quality. Repeatability and scalability follow.
Although using a support structure may play a role in building optimization, when the support structure supports almost all parts or when it is necessary to process internal geometries that cannot be processed after printing, it may become very expensive or even impossible to remove.
To avoid these challenges, training and reducing educational barriers are crucial.
These solutions include promoting application standards, out-of-the-box system fidelity, and improving end-to-end quality and software automation of the build process.
There are too many materials scientists, process technology experts, and PhDs handling daily projects with the hands of craftsmen. At the operational level, these misguided human assets lead to rising costs. This also divides pure R&D resources and slows down the widespread application of additive manufacturing.
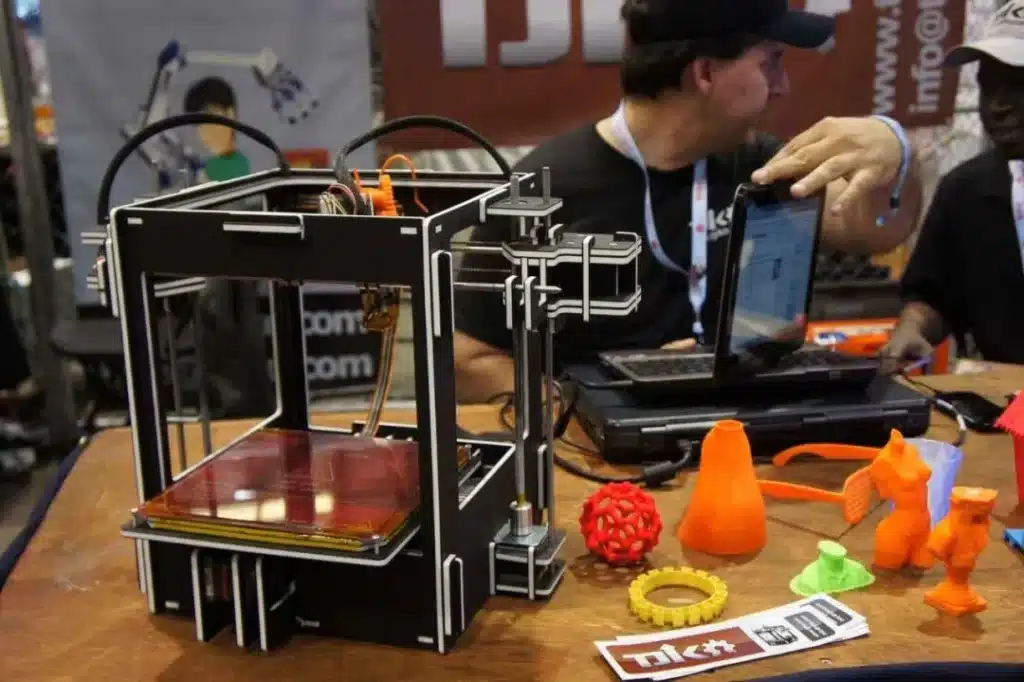
Looking ahead, it is beneficial to practice the “part integration and simplification” thinking mode in view of the labor force and excessive complexity existing in additive manufacturing. When the customer’s product design is placed in front of us, we certainly know what to do. Can we make more efforts to apply this knowledge to our own machines?
Making progress towards the success of CNC
Making additive manufacturing more like CNC machining is a realistic vision. CNC machines can easily achieve customization and medium-volume production, with repeatability, accuracy, and efficiency. It is the main force in the industry, and additive manufacturing has the potential to become the main force in the industry.
CNC is a model for applying automation, hardware and software integration, and improving economy, while also improving workshop performance.
If additive manufacturing can overcome its limitations, comply with stricter specifications, develop a unified parameter set, and improve automation, it can also reduce costs and simplify the identification of parts.
This will promote the supply chain to adopt this technology faster and improve scalability, which is eagerly expected from the MRO to aerospace or energy markets.